Dr.-Ing. Ali Montazeri
Contact
Dynamic programming is a mathematical optimization algorithm, which deals with problems where decision has to be made in stages. In this research, a time discrete-state dynamic programming model with finite horizon, which follows a recursive analytical approach in order to find the best sequence of decisions, will be used.
Research Objectives
The main objective in this research is to develop a finite control set model predictive controller based on dynamic programming, which further enhances the dynamic performance of asynchronous machine compared to standard controllers, while decreases the inverter’s switching and conduction losses. In addition, in order to decrease the copper and core losses in asynchronous machine, an optimized stator flux trajectory -in steady state and transient conditions is a matter of interest.
Furthermore, it will be investigated how to implement dynamic programming (as optimization algorithm) parallel with prediction algorithm which aims to avoid exponential increase of the prediction effort with increasing prediction horizon (Figure 2). Hence, it would be feasible to implement higher prediction horizons on standard computational hardware available for control of drives. A compromise between reasonable length of prediction horizon regarding future machine behavior and available computational platform has to be found.
A System on Chip (SoC) platform where the both processing system (microcontroller) and programmable logic (FPGA) are available can serve as an ideal computational platform for MPC controller. Because, the parallel computational power available on FPGAs can be utilized perfectly for parallel computation of prediction.
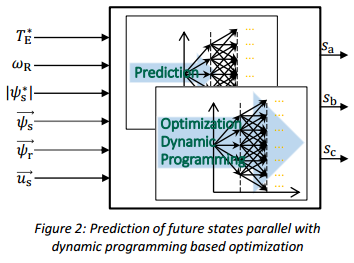
Project Partner
The project is funded by the German Research Foundation.