Nina Hatje M.Sc.
Contact
Multilevel converters for outer rotor flywheel energy storage systems
The electric machine of the outer-rotor flywheel energy storage system presents a unique set of challenges. The machine is housed in a high vacuum to reduce air friction losses thereby limiting the allowable losses in the rotor. The system operates with high rotational speeds and there are 4 or 5 pole pairs leading to the demand for high electrical output frequencies of the inverter. Additionally, due to the very high rotational speeds, the air gap increases considerably and the control algorithm needs to account for this. The inverter losses cannot be neglected in a FESS of this type and there is room for optimisation.
Multiple multilevel topologies will be compared with each other. The performance will be determined based on the total efficiency, the total costs and the distortion of the phase currents. A particular focus is the minimisation of the losses in the rotor.
The interaction and control of the shared neutral point of two multilevel converters will also be investigated.
Research Project
Project KoREV – SMS2
Cost reduction and increase of availability and efficiency of outer-rotor flywheel technology
Flywheel technology in outer-rotor form promise a higher energy density and a higher energy conversion efficiency at lower acquisition costs compared to the conventional structure.
This project aims to develop the technology further to become a close to the market energy storage system. The three key aims are to reduce the acquisition costs, increase the availability and to improve the efficiency of this innovative, highly integrated system. This research project builds on the previous research project of the same name (KoREV-SMS). The total efficiency aspect em
Project focus at the Institute for Power Electronics
The Institute is leading 3 of the 11 subprojects.
Dynamic Load Flow Coordination
To provide highly dynamic grid operating reserve, the existing energy management system or the energy exchange between flywheel and grid is to be fundamentally revised. The goal is the identification of an appropriate control structure which optimally coordinates the grid and machine control inputs. The provision of real and reactive power should occur within milliseconds and support the stabilisation of the power grid (“virtual inertia”).
Design and Construction of Machine and Grid Side Converter
An examination of the minimisation of air gap losses in the electrical machine through the choice of power electronics and topology. Potential Topologies will be designed and compared via simulations and assessed via total efficiency, total costs and distortion in the air gap field.
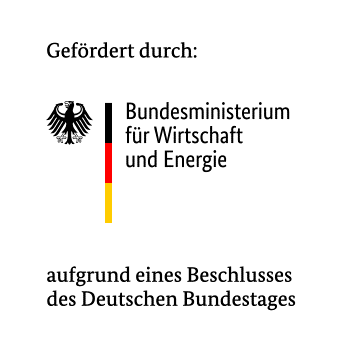