Philipp Kappes M.Sc.
Contact
philipp.kappes@pe-systems.de
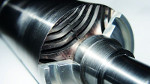
The operating principle of synchronous reluctance machines is already known for many years, but so far this type of machine did not become popular, because for operation without an additional cage, an inverter is required. The advantage of the synchronous reluctance machines with respect to the asynchronous machines is that with the same stator configuration no copper or aluminum is needed in the rotor. Hence a very simple and robust rotor setup is possible. Due to the absence of current flow in the rotor, the rotor losses are decreased. A higher efficiency compared to the asynchronous machine is possible at the expense of a higher magnetizing current in the stator.
For the operation of synchronous reluctance machines, the electric rotor position is needed. To increase the robustness and reliability of drive systems and to decrease the wiring effort, methods to estimate the rotor position from measured electrical quantities are developed and investigated since several years. The redundant position sensor can so be replaced by such a method.
Project Focus
Within the project various methods of sensorless control of synchronous reluctance-machines are compared and optimized with respect to the application field of positioning and servo-motors. Crucial for the achievable dynamic in this case is the behavior of the estimation method in the transient case, e.g. variable speed or load. Possible approaches are to integrate the transient behavior of the inverter into the estimation of the rotor position and the extraction of additional information by an oversampling of the stator currents.
In a further focus the fault tolerance of the estimated rotor position shall be investigated. The aim is to evaluate the deviation of the measured rotor position as a function of the speed. Such characteristics ca be used for systems where redundant position sensors are required for safety reasons to provide a robust and automatic fault detection. With a sensorless estimation method the redundant position sensor can be resigned.
Project Funding and Partner
The project is funded in the context of the “Zentralen Innovationsprogramms Mittelstand (ZIM)” by the Federal Ministry of Economics and Energy as a “ZIM-Kooperationsprojekt”. The project partner is the ESR Dipl.-Ing. Pollmeier GmbH – Servo Antriebstechnik located in Ober-Ramstadt.